Aus der Geschichte Friedrichsholms
Von Hans-Werner Möhrs
Die Lage Friedrichsholms
Friedrichsholm liegt auf einer Inselmoräne im Urstromtal der Eider. Der höchste Punkt des Dorfes ragt 12m über den Meeresspiegel empor. Der Hügel ist zum größten Teil von Grünland umgeben, auf dem die Viehhaltung die größte Rolle spielt und der Ackerbau nur gering ist. Es ist dasselbe Land. auf dem vor zweihundert Jahren Menschen aus Süddeutschland ihr mühseliges Werk begannen.
Die Verkehrslage des Dorfes ist heute recht gut. Es liegt an der Bundesstraße 202 zwischen Rendsburg und Friedrichstadt. Die Kreisstadt Rendsburg ist nur 18 km entfernt und daher leicht zu erreichen.
Zwei Unternehmen, die die Entwicklung des Dorfes entscheidend beeinflußt haben, waren die Ziegelei und die Glasfabrik.
Die Ziegelei
Viereinhalb Jahrzehnte sind vergangen, seitdem die Friedrichsholmer Ziegelei ihre Arbeit eingestellt hat. Nur noch einige Spuren erzählen uns heute von dem, was einstmals war. Das Anwachsen einer beachtlichen industriellen Konkurrenz hat diesen Betrieb zum Erliegen gebracht.
Die Ziegelei wurde 1868 von Friedrich Haß aus Holzbunge, der sich hier mit seiner Familie ansiedelte, errichtet. Da Friedrich Haß die Ziegelarbeit nicht richtig verstand, mußte er einen Ziegelmeister einstellen. Sein Sohn Josias mußte das Ziegeleihandwerk gründlich erlernen, und dieser hat dann mit 21 Jahren den väterlichen Betrieb übernommen. Die älteren Leute im Dorfe, die noch mit Josias Haß zusammengearbeitet haben, erzählen, daß er sein Handwerk ausgezeichnet verstanden habe. Unter seiner Führung kam die Ziegelei zur vollsten Blüte.
a) Herstellung der Steine und der Röhren
Die ersten Brände waren sehr primitiv, es waren Feldbrände, d. h. die Steine wurden unter freiem Himmel in der Form eines Ofens aufgesetzt und gebrannt. Josias Haß ließ 1875 einen Ofen aus Steinen aufmauern. Der Ofen, der 8 m lang, 6 m breit und 4 m hoch war, verjüngte sich nach oben. An beiden Längsseiten befanden sich 8 Feuerlöcher, die ungefähr die Höhe eines normalgroßen Mannes hatten.
Die alten Leute des Dorfes erzählen den Werdegang der Steine folgendermaßen: Der Lehm wurde aus der Grube mit einer Lore herausgeholt und in einen großen Schlammtopf gekippt. In diesem Topf, der 50 cm in der Erde saß, wurde der Lehm mit Wasser gut vermengt. Das Wasser mußte unter großem Kraftaufwand mit der Hand gepumpt werden. Bei dieser schweren Arbeit
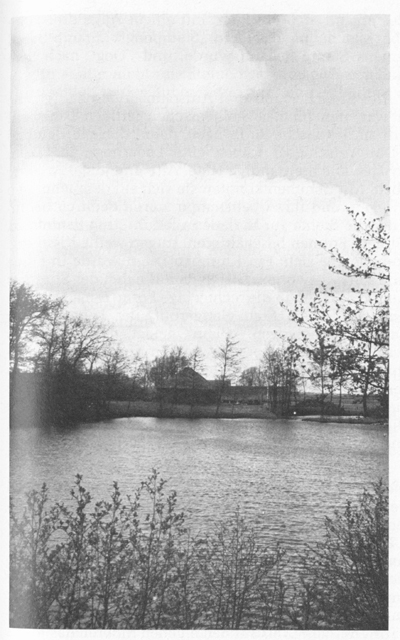
Abbildung 1: Im Vordergrund sieht man die Ziegeleikuhle und im Hintergrund die Trockenscheunen
wurden die Männer oft abgelöst. Nach einer gewissen Zeit wurde die flüssige Masse in drei tiefergelegene Töpfe abgelassen. Diese Töpfe waren unterirdisch drainiert. so daß das Wasser in den Sand versickern konnte und der Lehm sich am Boden ablagerte. So mußte der Lehm einen halben Tag liegen. Damit er nicht ganz austrocknete, deckte man die sogenannten Schmiertöpfe mit Blechplatten zu. Anschließend wurde der Lehm mit Karren in einen anderen Topf befördert, in dem er dann für das Steinemachen hergerichtet wurde.
Mit einem Gestell, das von zwei Pferden einen halben Tag gezogen wurde, vermischte man den Lehm mit Wasser. Dieses Gestell nannte man allgemein die "Störtkorr". Die Pferde trugen hierbei Schutzbrillen. Durch die verschiedenen Mergelsorten war es möglich, rote, gelbe und weiße Steine herzustellen. Ein alter Einwohner des Dorfes erzählt, daß ein Pferd mit einem Auge drei Jahre diese Arbeit verrichtet habe. Man nannte das Pferd "Stampoog". "Stamp", weil es von einem Bauern namens Stamp gekauft wurde, und "Oog" nach dem auffallenden Merkmal des einen Auges.
Bei der Ziegelei waren drei Streicher und drei Aufschieber beschäftigt. Die Aufgabe der Aufschieber war, den für das Steinemachen fertigen Lehm auf einem Brett den Streichern an die Tische zu bringen, damit diese fortlaufend weiterarbeiten konnten. Die Aufschieber trugen eine Lederhose, und zum Schutz gegen die Sonne trugen alle breitrandige Hüte. Alte und junge Arbeiter gingen barfuß bei der Arbeit. Mit Schuhen konnten sie sich auf dem lehmigen Boden nur schwer fortbewegen, und ihr Arbeitstempo wurde dadurch behindert. Nur der Fuhrmann, der die Steine zur Verladestelle fuhr, trug Pantoffeln. Die Streicher, die sich mit dem Formen beschäftigten, trugen weiße Kleidung. Das Formen der Steine ging so vor sich: Ein Klumpen Lehm wurde in einen Wassertrog, der in der Nähe stand, geworfen. Gleich darauf nahm der Streicher den Lehm wieder heraus und preßte ihn in die rechteckige Form. Danach wurde die Oberfläche des Lehms mit einem Stab glattgerollt, der Lehm wieder herausgenommen und flach auf eine sogen. "Bahn" gelegt, die mit feinem gelben Sand überstreut war. In der Ziegelsprache wurden die Steine "getummelt". Nach ungefähr 3 bis 4 Tagen, wenn die Steine das Anfassen vertragen konnten, wurden sie gereinigt. Diese Reinigungsarbeit verrichtete lange Jahre hindurch Frau Margarethe Brügmann. Mit einem abgebrochenen Sensenstück schabte sie alle Unebenheiten, wie Sand und Kies, von den Steinen. Nach diesem Reinigungsvorgang kamen die Steine 6 bis 14 Tage in die Trockenscheune.
Wenn genügend Steine fertig waren, wurde der Ofen für einen Brand hergerichtet. Nachdem die Steine, ungefähr 70 000 bis 80 000, ordnungsgemäß in den Ofen gesetzt waren, werden die 8 Feuerlöcher mit Torf zugepackt, der dann angezündet wurde. Ein Brand dauerte 9 Tage. Der Ofen mußte Tag und Nacht unter Feuer gehalten werden. Die ersten 4 Tage des Heizens nannte man "Schmohfür", die restlichen "Fullfür". In der Regel benötigte man bei "Schmohfür" einen Mann und bei "Fullfür" zwei Männer. Bei "Fullfür" mußten beide Männer von jeder Seite des Ofens zugleich heizen. Das Brennmaterial war hauptsächlich Torf, der zum Teil auf den eigenen Mooren des Josias Haß gegraben und getrocknet wurde. Der restliche Torf wurde von den Dorfbewohnern gekauft. Später feuerte man außer Torf noch Holz und Steinkohle. Für einen Brand benötigte man drei Wagen Torf. An den bläulichen Flammen, die in den letzten drei Tagen aus dem Ofen schlugen, erkannte man. daß die Steine "gar" waren.
Dann mauerte man die Feuerlöcher zu, damit die Steine langsam abkühlen konnten. Nach vier Tagen schoben die "Puttschuwer" die Steine aus dem Ofen und sortierten sie. Die Steine, die in der Nähe des Feuers gelegen hatten, wurden billiger verkauft. Im Sommer zogen viele Saisonarbeiter von Rhein und von der Weser nach hier, um in der Ziegelei zu arbeiten. Die Arbeit in der Ziegelei war schwer, weil keine Maschinen vorhanden waren und alles mit der Hand betrieben wurde. Pünktlich um 4 Uhr weckte ein Nachtwächter die Arbeiter. Nach einem gemeinsamen Morgenkaffee bei dem Besitzer wurde die Arbeit aufgenommen. Um 19 Uhr war für den ersten Teil der Arbeiter Feierabend. Nur die Heizer hatten Nachtschicht; sie wurden jedoch um 12 Uhr abgelöst.
Man stellte nicht nur Steine her. sondern auch Röhren in allen Größen. Der Unterschied in der Zubereitung des Lehmes lag nur darin, daß der Lehm zum Schluß in einer besonders dafür geeigneten Mühle gemahlen wurde. In einem besonders großen Topf wurde der Lehm dann wieder mit Wasser gut vermischt. Diese Masse preßte man in runde oder viereckige Röhrenformen. Mit einem langen Draht schob man die nassen Röhren auf einen außergewöhnlich langen Tisch, wo sie mit einer sogen. "Gaffel" in einer bestimmten Länge geschnitten wurden. Die Röhren mußten 8 Tage gebrannt werden.
b) Verkauf der Steine und Röhren
Die fertigen Steine und Röhren wurden aufgestapelt und mit Blechplatten überdeckt. Laufend gingen Aufträge aus den umliegenden Dörfern ein. Die Steine und Röhren wurden nicht nur mit Pferdefuhrwerken an den Bestimmungsort gefahren, sondern sie wurden auch, je nach Lage des Ortes, auf dem Wasserwege befördert. Friedrichsholm liegt günstig zur Sorge, die in die Eider mündet. An der Sorge befand sich die Verladestelle, von der jetzt noch Überreste sichtbar sind. Schuljungen fuhren die bestellten Steine an die Verladestelle bei der Töpferei oder "Püttjerie", wie wir sie in der plattdeutschen Sprache nennen. Die Kutscher mußten besonders vorsichtig sein, weil die letzte Strecke des Weges abschüssig war. Nach dem Unglück mit einem Schuljungen aus Grevenhorst fuhr Josias Haß selbst die Steine zur Verladestelle. Nach damaligen Verhältnissen wurden die Steine gut bezahlt. Der Besitzer Haß erhielt für 100 Stück achtzöllige Steine 11 Mark, für ebenfalls 100 Stück zehnzöllige 18 Mark. Die Röhren wurden für etwa 15 Mark verkauft.
c) Was ist aus dem Betrieb geworden?
Im Jahre 1900 übernahm Josias Haß' Sohn Christian den Betrieb. Er führte das Werk würdig fort. In den Jahren des ersten Weltkrieges (1914-1918) mußte die Arbeit häufig unterbrochen werden. So blieb zu Anfang des Krieges ein Ofen mit fertiggebrannten Steinen stehen. Es war kein geeigneter Mann mehr vorhanden, der die Steine und Röhren ordnungsgemäß herausholen konnte. Dieser Ofen wurde erst am Ende des Krieges von Christian Haß geleert. In den ersten Nachkriegsjahren wurden nur drei Brände hergestellt. Im allgemeinen betrug sonst die durchschnittliche jährliche Leistung vier bis fünf Brände. In einem Sommer konnte man sogar sieben Brände verzeichnen. Diese Höchstzahl hat man nie wieder erreicht. Bald stellte man die ersten Maschinen her, und so konnten die Steine schneller und billiger hergestellt werden. Für kleinere und mittlere Betriebe waren diese Maschinen jedoch zu teuer. Durch die Maschinenarbeit der großen Betriebe nahm der Absatz zu. So entschloß man sich im Jahre 1933, die Ziegelei aufzugeben. Den letzten Brand benutzte Christian Haß für den Hausbau seines Sohnes Heinrich. 1933 brach man das Wahrzeichen der Ziegelei, den Ofen. ab. Die Windmühle, die vom Herbst bis zum Frühling das überschüssige Wasser aus der Kuhle pumpte, wurde erst 1938 entfernt. Nur die Trockenscheunen standen bis vor einigen Jahren. Sie wurden vom Bauern Friedrich Haß als Geräteschuppen benutzt.
Abbildung 2: Trockenscheunen - bis auf den Rundteil verfallen
Abbildung 3: Trockenscheunen - bis auf den Rundteil verfallen
Abbildung 4: Trockenscheunen heute
Abbildung 5: Standort der früheren Glasfabrik
Die Glasfabrik
Als 1896 der große Fabrikschornstein der Glasfabrik, ein Wahrzeichen des Dorfes Friedrichsholm, abgerissen wurde, war es ein großes Ereignis. Sogar die Schulkinder des Dorfes durften den Abbau miterleben. Mit diesem Abbruch schloß ein kleines Industrieunternehmen seine Pforten. Es hatte seit 1842 bestanden und vielen Arbeit gegeben und war weit im Lande bekannt. Das Bild zeigt den Bauernhof, wo früher die Fabrik gestanden hat.
Ungefähr fünfzig große, kräftige Männer, Glasbläser, Torfgräber, Glasmacher, Fuhrleute und Heizer bildeten den Stamm der Fabrik, die ein Glasarbeiter, Petov mit Namen, aufgebaut hatte. Anfangs ging er selbst von Dorf zu Dorf und verkaufte seine Waren. Später wuchs der Betrieb, und gelernte Glasbläser aus Brandenburg halfen ihm in der Herstellung seines Weiß- und Grünglases. Folgende Namen seiner Mitarbeiter sind heute noch bekannt, obwohl kaum noch eine Familie im Dorfe lebt: Glasmacher Ludwig Stoor, Adolf und Fritz Stoor, Ferdinand Götzmann, Ludwig Hawes, Glasarbeiter Göbel, Hans Ohm, der Meister Friedrich Ruhländer (die Familie wohnt noch im Dorf) und der Glasfuhrmann Heuck.
Der alte Petov war ein guter Kaufmann, der mit einer Unterstützung von 500 Talern, die der Bauherr und Zimmermann Timm Sievers als Anteil gab, die Fabrik ins Leben rief. Mergel und Sand bezog man aus der Umgebung, obgleich der Pahlhuder Mergel recht steinig war.
Die Fabrikationsmethode war nur so weit bekannt, daß man wußte, daß das Friedrichsholmer Glas aus sieben verschiedenen Teilen gemacht wurde. In 6 "Putten" wurde das Gemenge von je zwei Mann eingeschaufelt. Diese Gefäße hatten Waschkesselgröße. Morgens um 2 Uhr war das Gemenge "blank", und es kam mit langen "Pipen" in die Form. Man machte Medizingläser, Flaschen und zuletzt große Korbflaschen, für die das erforderliche Flechtwerk in Heimarbeit hergestellt wurde. So bot diese Arbeit noch eine weitere Verdienstmöglichkeit.
Das Weißglas wurde ohne Zusatz von Braunstein hergestellt. Alle Jahre wurde ein Glasofen ausgelöscht und ein neuer in 4 bis 6 Wochen aufgebaut. In den letzten Jahren arbeitete man mit Torfgas, das in einer kleinen Gasanstalt hergestellt wurde. Nachdem das Geschäft gut angelaufen war, zahlte der alte Petov den Mitinhaber Sievers mit 3000 Talern aus. Dieser zog dann nach Amerika. Die Prinzenmoorer Glasfabrik wurde aufgekauft, und so blieb die Friedrichsholmer Fabrik, die große Reingewinne abwarf, leistungs- und konkurrenzfähig. Die fertige Ware wurde mit Fuhrwerken durch das ganze Land gefahren. Im Süden kam man bis nach Hamburg und im Norden bis nach Hadersleben. Das war bei den Wegeverhältnissen in damaliger Zeit nicht immer ein leichtes Unternehmen. Auf diesen Reisen wurden auch Scherben eingekauft, die man in der Fabrik einschmolz.
Nach dem Tode des alten Petov führten anfangs die beiden Söhne Karl und Eduard die Glasfabrik weiter.
1894 verkaufte Karl Petov die Fabrik an eine Hamburger Firma (Nagel AG), die den Betrieb in Friedrichsholm auflöste und das dazugehörige Land aufteilte. Die vielen fremden Glasarbeiter verließen mit der Betriebseinstellung das Dorf. Nur wenige dieser Familien sind heute noch in Friedrichsholm ansässig.